By Blair Loftis, national director of power generation and transmission for Terracon
Does uncertainty in the market have you frustrated? When things get tough, it is sometimes best to focus on simple things like bricks and mortar—or, maybe, a better way to reduce risk in tracker foundation design.
So what makes developing and constructing a utility-scale solar project so complicated? Consider these factors:
- the parlay known as contract origination;
- interconnection requirements that vary dramatically across America’s six independent system operators (ISOs), seven regional transmission operators (RTOs) and multiple individual utilities or utility holding companies;
- land-use permitting and approvals that share few similarities from one agency having jurisdiction (AHJ) to the next;
- project design, which must keep pace with innovations in critical system components;
- strategic procurement sourcing; and
- constant challenges related to construction, commissioning, legal, insurance, renewable energy credit arbitrage and financing.
With a list like this, it helps to focus on the end goal: providing solar energy at a competitive price point. We must work to ensure that a profitable solar power purchase agreement (PPA) does not become the virtual unicorn of power marketing. I propose focusing on what we can control, and minimizing the uncertainty related to tracker foundation design is a great way to reduce risk and save money.
Clik here to view.
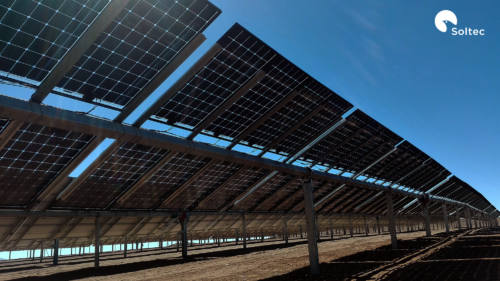
A horizontal single-axis tracker from Soltec
Consider this example. The horizontal single-axis tracker has become the industry standard for utility-scale installations. Design specifications vary by manufacturer, but we can assume an installation rate of 750 posts per megawatt. Extrapolate that rate to a mid-size solar plant (50 MWdc) and you will install nearly 40,000 individual foundation posts. The average post embedment depth is no greater than 8 ft. This hypothetical project would require over 57 linear miles of steel for the foundations. If you could shave 2 ft off the embedment depth, how much would you save by reducing 15 miles of steel? Somewhere around $750,000, for a fairly modest project. If we take it to 300 MWdc, the savings could be approximately $5 million.
Overlooking this potential cost savings doesn’t make any sense considering the tracker makes up nearly 25% of the balance of system (BOS) cost, and the tracker foundations are a substantial part of that. Even more concerning, the foundation costs are the big unknown. You can’t easily estimate foundation costs during project development and, more importantly, when you are in the middle of PPA negotiations. On past projects, we have seen the foundation installation depth be a deal breaker.
The evil cousin of depth is construction means and methods. For example, what if the project requires pre-drilling, over drilling, drilling and grouting or soil stabilization to secure the foundations? What about expansive clays, frost action or karst? The possible uncertainties can make the most solar-savvy squirm.
Today, we know variances in foundation depth can mean a total forfeit of profit. A decade ago, little thought was given to the depth of the foundation post. It just didn’t have much impact on profits. Still, in the interest of maximizing investment return, we began developing a process to remove uncertainty around post depth and the means in which they would be installed. Over the years, I have worked across the industry and have had the opportunity to refine this simple process which has been adopted by some of the leading developers of utility-scale solar projects in North America.
This process, coined “A Gate-Stop Approach to Solar Foundation Design” proceeds as follows:
- Gate 1 – Desk Top Review: Evaluate near-surface soil conditions and expected geological conditions from a review of available public data. If the review suggests unfavorable conditions (e.g., shallow bedrock), then consider another site. If the data is uncertain, then pass through the gate and proceed to a preliminary site investigation.Most geotechnical, architectural or engineering firms can perform this service and have adapted sophisticated platforms through ArcGIS which include interactive interfaces and user-friendly platforms. The key is the geotechnical engineer’s evaluation of the data. The data is the constant variable, as virtually everyone relies upon the same data set. The difference for us is Terracon’s unique approach.
Terracon has created a report of expected geotechnical conditions (REGC), which supplements the often high-level, summarized data available in the public domain with real exploration data we have collected over decades of projects. We have invested in digitizing this data so that it is searchable by GPS coordinates and can be filtered based upon specific search criteria.
- Gate 2 – Preliminary Site Investigation: Using what we have learned passing through Gate 1, our geotechnical staff develops a smart work plan to confirm project expectations. The work plan may involve test pits, soil borings, soil probes or cone penetration tests. We know what we expect to encounter and tailor the work plan accordingly. At this point, there is heavy reliance upon observations such as what can be seen from an open pit or a soil boring or CPT log. Bulk or discrete samples should be obtained and stored, but testing comes later. If no obvious concerns are revealed from this observatory phase, then pass through Gate 2 and proceed to a preliminary design evaluation.Terracon has developed a formulaic approach to the investigative frequency or recommended number of exploration locations per acre of proposed development. Upon completion of the REGC, we revise that frequency to fit the specific project site based upon our confidence assessment of the public data adjusted by our relevant proprietary data. The more data points from prior projects proximal to the site of interest, the higher the confidence interval assigned to the public data. We call this a SMART Characterization Plan.
- Gate 3 – Preliminary Design Evaluation: This is a means to an end. Ultimately, a barrage of soil testing will be required for a multitude of design requirements. The objective is to collect sufficient volume of samples prior to passing through Gate 2, but not to spend the money on all of the required testing until needed. Only a few simple tests to perform a preliminary L-Pile analysis are needed. This will provide an opportunity to estimate a range for the maximum and minimum foundation embedment depth. If this depth interval is within project margins, then proceed to Gate 4, design optimization.Here, our REGC really meets its return on investment. Through our extensive database, we are often able to extract the data necessary to perform this preliminary L-Pile analysis without collecting site samples, or significantly reducing the frequency of samples required.
- Gate 4 – Design Optimization: Now we are at the threshold between theory and practice. This culminates with the installation of test piles and pull testing (lateral and axial) to agreed load levels. From these empirical results derived from expected construction conditions, the optimum design embedment depth can be determined.
What makes the Terracon approach different is our sequencing enhancement. In other words, not just how we do things, but when we do them. We provide an outline of gates with built in off-ramps so that project compatibility can be verified through an iterative process along critical decision points.
Blair Loftis is the national director of power generation and transmission for Terracon. Loftis brings to the position more than 25 years of industry leadership in consulting engineering, construction management, and electric utility management. His work in the areas of operations, strategy, project management, and finance bring a unique understanding to project development and meeting client objectives.
Image may be NSFW.Clik here to view.